Discover why millions of Dip-Tech Machinery printed automotive and transportation glass panels are already in use in a wide range of vehicles around the world. With a comprehensive automotive solution package, our machinery combined with a special set of inks meet the automotive industry’s most demanding standards and requirements for intensive mass production capacities.
Automotive
Digital Printing Solutions
Dedicated mass production solution for automotive, specialty transportation & other industrial printed applications
Dip-Tech Machinery printers are developed to print with world’s leading ceramic ink providers of automotive and transportation enamels. Our printers are designed and tested to print with a wide range of specially formulated ceramic automotive glass enamels and silver conductive pastes, suitable for tempering, lamination, sag or press bending and pre-firing. These enamels are specially designed to meet decorative specifications and to prevent degradation and delamination of vehicle glass adhesive from UV-light radiation, as required by automotive OEM and after-market industry specifications.
The choice between screen printing and digital printing is not a zero-sum game. Both offer excellent quality. In fact, digital and screen printing are often best used in tandem, allowing glass processors to shift between the formats according to need, to better utilize screen capacity, and fully maximize ROI. To enhance the learning process and ramp-up business, Dip-Tech Machinery provides you with the end-to-end support you need in order to deliver outstanding printed glass products and increase both your potential and market share.
Introducing VX-3, Dip-Tech Machinery's dedicated serial production technology for automotive, transportation and industrial ceramic ink printing. The new generation of Dip-Tech Machinery is the most advanced digital ceramic ink printing solution automotive. It offers turbo-charged throughput, superb quality, and a competitive ROI compared to screen printing. Capable to fully integrate in glass processing lines, it delivers cost-efficient, high-quality automotive glass printing, with quick and accurate registration on any glass shape – all at serial production speed.
Build your business with Dip-Tech Machinery Technology
Glass Types
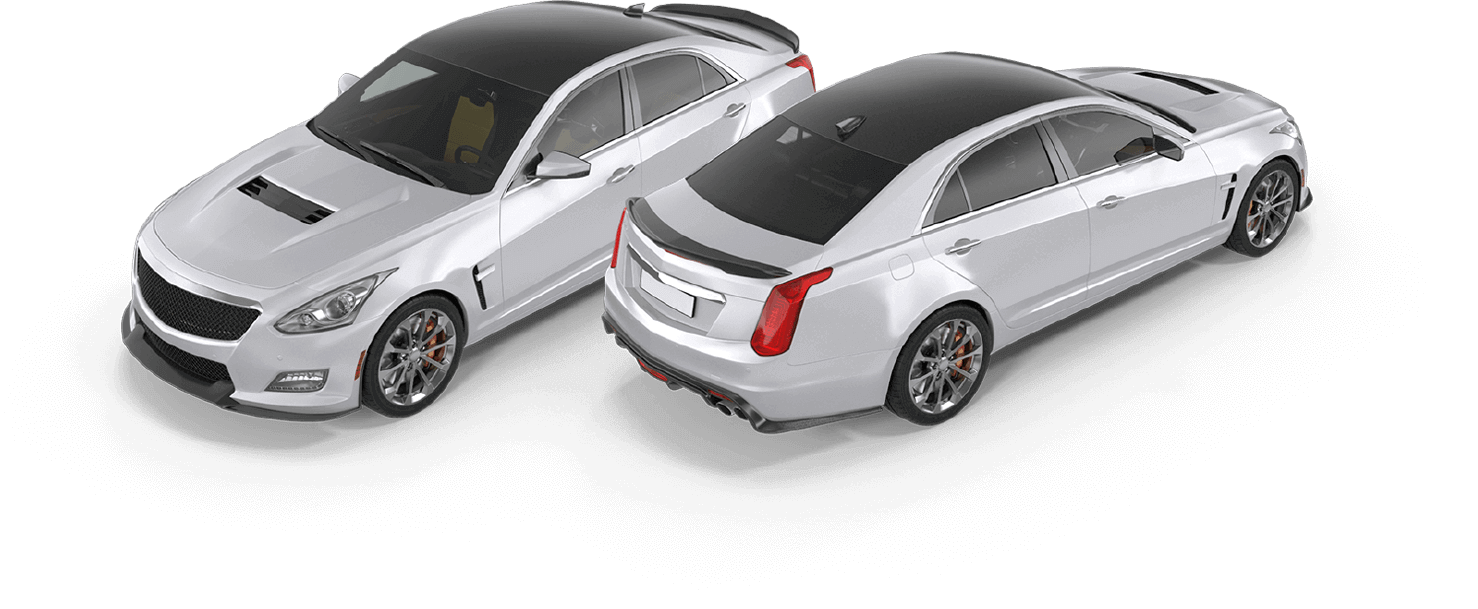
ROOF GLASS
Automotive Black Digital Ink (72 hours test) or Automotive Anti-Stick Black Digital Ink
- UV filtration
- Hard coating compatibility
WINDSHIELD
Automotive Black Digital Ink (72 hours test)
- Automotive Anti-Stick Black Digital Ink for press bending process
- Raster patterns
- Frames
- Logos
- Barcodes
Automotive Conductive Silver Digital Ink
- Camera wiring
- Radar wiring
- Wiper demisters
- Sensors wiring
BACKLIGHT
Automotive Anti-Stick Black Digital Ink for press bending (72 hours test)
- Frames
- Logos
- Barcodes
Automotive Conductive Silver Digital Ink
- Fine lines
- Bus bars
- Wiper demisters
- Sensors
- Defrost systems
DOOR GLASS
Automotive Black Digital Ink (72 hours test) or Automotive Anti-Stick Black Digital Ink
- Frames
- Logos
- Barcodes
QUARTER GLASS
Automotive Black Digital Ink (72 hours test) or Automotive Anti-Stick Black Digital Ink
- Frames
- Logos
- Barcodes
Automotive Raster Master
An innovative tool which Interfaces with AutoCAD and assists to create gradient raster pattern for automotive / transportation black frame drawings. The tool can automatically:
- create raster grid to all frame designs
- provides seamless raster arrangement in corners, curves and special fill area on the CAD
- Replaces tedious corrections of manually generated raster patterns
Dynamic Index system
Dip-Tech Machinery VX-3 printer is designed for the unique requirements of the specialty transportation industry. It includes an inline automatic indexing system that enables to register a wide variety of glass shapes and sizes, allowing for a fast and user-friendly setup.
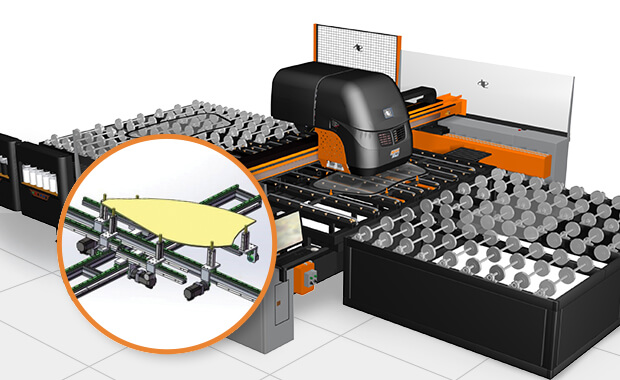
Make digital glass printing for serial production your advantage
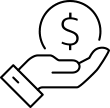
Cost savings
- Save screen purchase costs
- More space in the factory
- Zero screen preparation and reduced post-print cleaning
- Reduced labor, with a single operator
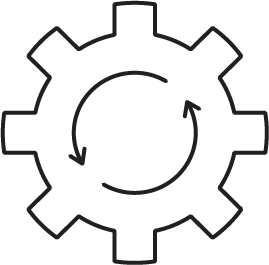
Efficiency
- Eliminating the screen's setup time
- change production models with just a few mouse clicks
- Fully integrated and with your production line
- High print quality and accuracy
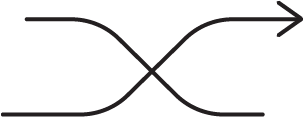
Flexibility
- Suitable for varied processes – Firing, tempering or bending
- Easy file preparation and customization, easy sampling
- Full control over wet layer thickness, with easy customization
- Enables variable data printing – For batch number or QR code
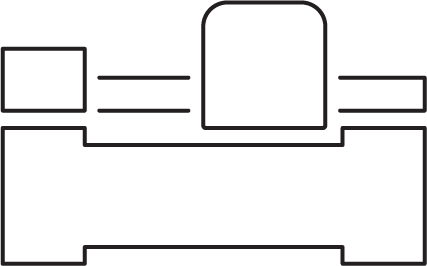
Improved printed product
- Lower enamel surface roughness – Better glass strength
- Minimal printer setup enables easy adding of a second color
- Short lead time for sampling
Recommended Applications
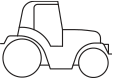
Agricultural, construction & specialty vehicles
The special transportation industry has a unique set of glass demands. Whether it’s laminated glass for rough and tough terrain, or windshield repair you need Dip-Tech Machinery digital glass printing offers the dedicated serial production solution for your agriculture, construction and specialty vehicle demands. read more
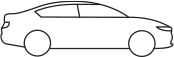
Automotive replacement glass
Whether you need windshield replacement, car window repair, or general car glass, Dip-Tech Machinery dedicated serial production solution for automotive is the answer for you. Fully automated and inline, Dip-Tech Machinery printers offers the most advanced digital system for automatic indexing of glass registration, with no manual operation required. read more
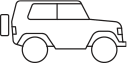
Bulletproof & protective vehicles glass
With our expertise in digital glass printing, Dip-Tech Machinery is proud to supply the dedicated serial production technology needed for the bullet-resistant glass required of civilian and military applications. Effectively serving as a glass protector, our digitally printed laminated glass can be used for windscreen replacement, windshield crack repair, or any functionality where auto glass is needed. read more
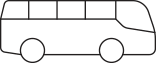
Buses & RV
The special transportation industry has a unique set of glass demands. Whether it’s laminated glass for rough and tough terrain, or windshield repair you need Dip-Tech Machinery digital glass printing offers the dedicated serial production solution for your agriculture, construction and specialty vehicle demands. read more
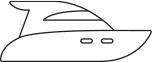
Marine glazing & yacht interiors
At Dip-Tech Machinery, we’re proud to offer a truly innovative, high-tech solution dedicated to marine glass and windows. Both attractive and functional, Dip-Tech Machinery digitally printed glass is perfect for multiple purposes, from replacement glass to glass repairs. read more
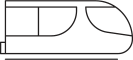
Rail transport
With increased urbanization and environmental consciousness, the passenger transport sector is a growing market around the world. In fact, rail transport, buses, and coaches are one of the fastest growing glass markets. read more